The Carbon Footprint of Steel: Decarbonisation Is Critical
Source: Caisin Global
16 September 2024 – by Eric Koons
Steel is the backbone of modern infrastructure, essential in everything from buildings to vehicles. Steel demand is growing. However, the carbon footprint associated with steel production to meet global demand is substantial, contributing nearly 8% of global carbon dioxide (CO2) emissions.
Decarbonising the steel industry is critical for achieving global climate goals, and it falls on steel producers and steel-using companies to drive this transition. For example, Hyundai Steel is among the world’s top 50 steel producers, generating 19.24 million tonnes annually.
However, it produces all of its steel with fossil fuel-reliant operations, which trickle down to companies in the automotive industry in South Korea, such as Hyundai-Kia. For Hyundai-Kia, this limits its ability to access low-carbon steel in pursuit of its 2045 net-zero goal.
Decarbonising the steel industry requires a push from companies along all levels of the supply chain to be successful.
Steel’s Carbon Footprint
Steel Carbon Dioxide Emissions
Steel production is highly energy-intensive and fossil fuel-reliant, and coal accounts for 70% of the total feedstock used in the industry. This results in traditional steel production methods like blast furnaces emitting around 2.33 tonnes of CO2 per tonne of crude steel production in 2022. However, modern methods like electric arc furnaces are significantly lower, at 0.68 tonnes of CO2 per ton of steel.
This stark difference highlights the potential for reducing the carbon footprint of steel by adopting more efficient production technologies.
Global Steel Emissions
The steel industry contributes approximately 3.6 gigatonnes of global carbon emissions annually, including indirect emissions. This makes primary steel production one of the largest industrial sources of carbon emissions worldwide. For comparison, steel production releases more CO2 than powering all of the world’s commercial structures and is only slightly less than what is produced by all road transportation.
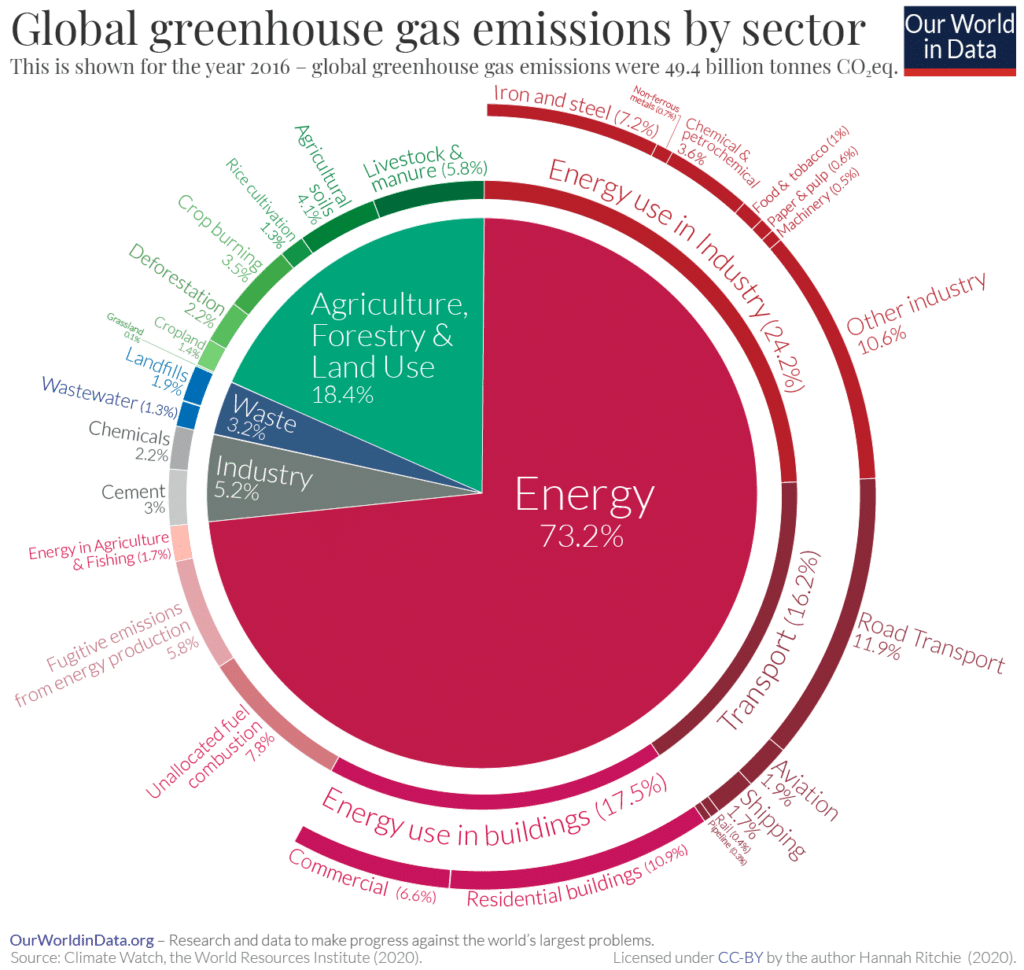
What Drives Steel’s Carbon Footprint
The steel production process is energy-intensive and consists of several key stages. It begins with extracting and processing raw materials, primarily iron ore and coal. This stage accounts for approximately 9% of the total energy consumption in steel production.
Blast Furnaces Versus Electric Arc Furnaces
The most common production method is the Blast Furnace-Basic Oxygen Furnace (BF-BOF) process. The BF-BOF process involves feeding iron ore and coke, a material derived from coal, into a blast furnace. In the furnace, coke acts as both a fuel and a reducing agent, converting iron ore into molten iron by removing oxygen. This molten iron is then transferred to the BF-BOF, where pure oxygen is blown through it, reducing impurities and producing steel. BF-BOF accounts for 75% of global steel production.
In contrast, electric arc furnaces (EAFs) are a more sustainable steel production process, primarily using recycled scrap steel rather than raw iron ore. An electric arc furnace operates by generating electric arcs between graphite electrodes to melt the scrap steel, a process that requires significantly less energy than traditional methods.
EAFs also offer flexibility in production and can be powered by renewable electricity, further lowering their carbon footprint. However, the process needs to be further decarbonised with green electricity. EAFs currently account for about 25% of global steel production.
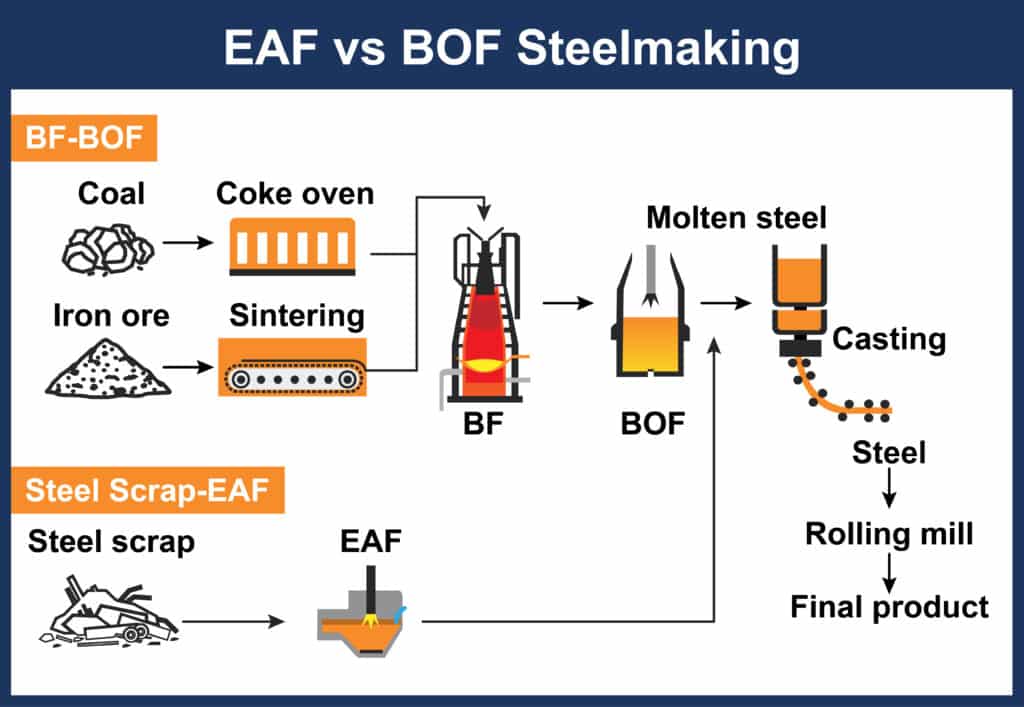
The Impact of Steel Transportation
Transportation and logistics also add to the carbon footprint, especially when raw materials and finished products are shipped long distances. The entire transportation process relies heavily on fossil fuels, from mining operations powered by diesel to transporting raw materials by ships, trains and trucks.
Reducing transportation’s carbon intensity – whether through the adoption of renewable energy, improved energy efficiency or a shift to low-carbon transportation – is essential for lowering the steel industry’s overall carbon emissions.
Technology Landscape for Decarbonising Iron and Steel Production
What Is Green Steel?
Green steel produces significantly fewer greenhouse gas emissions than traditional production processes. Key strategies include using EAFs, integrating green hydrogen as a reducing agent and harnessing renewable energy. Recycled steel produced via EAFs also qualifies as low-carbon due to its significantly lower emissions.
The Role of Recycled Steel
Recycling steel is one of the most effective ways to reduce the carbon footprint as the steel can be made with an EAF. Moreover, recycling steel conserves natural resources. For every tonne of recycled steel, approximately 1.5 tonnes of iron ore and 0.5 tonnes of coal are saved, reducing the need for mining and the associated environmental degradation. Energy consumption is also significantly lower. Recycled steel production uses about one-eighth of the energy used to produce steel from raw materials.
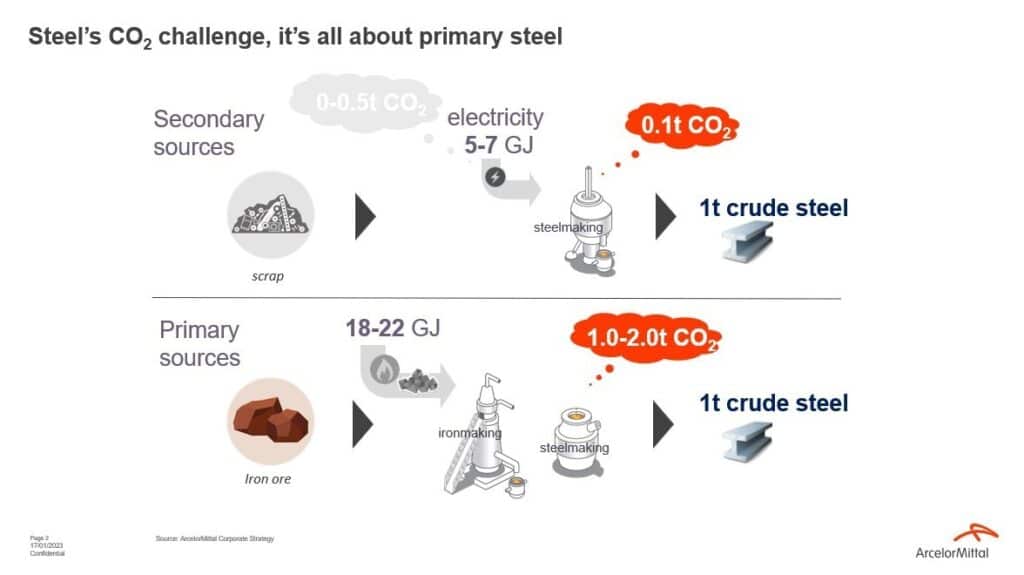
Despite its benefits, challenges persist, including the limited availability of high-quality scrap steel and inefficiencies in collection and sorting. To fully capitalise on recycled steel’s potential, the industry must improve recycling infrastructure and invest in technologies that enhance the quality and efficiency of recycled steel production.
Green Hydrogen for Converting Iron Ore into Steel
Green hydrogen is emerging as a promising technology for low carbon steel production. This process involves using green hydrogen from electrolysis powered by renewable energy sources, as a reducing agent to convert iron ore into steel. Unlike traditional methods that rely on coke, which emits large amounts of CO2, green hydrogen only produces water vapour as a byproduct.
One notable example is the HYBRIT project in Sweden, which uses hydrogen and renewable energy. HYBRIT aims to produce fossil-free steel by 2026, potentially reducing Sweden’s CO2 emissions by 10%.
Although still in its early stages and currently more expensive than conventional methods, green hydrogen-based steel production represents a crucial step toward achieving net-zero emissions in the steel industry by 2050.
A Greener Path Forward for the Steel Industry
The steel industry’s substantial carbon footprint makes it a critical focus area for global decarbonisation efforts and meeting the Paris Agreement. The steel sector needs to cut its emissions by at least 91% by 2050 to stay within the 1.5°C warming limit.
Global leaders in steel production are already setting examples by adopting innovative technologies like EAFs, green hydrogen and renewable energy. The rest of the industry must learn from these examples and accelerate the adoption of such practices to reduce emissions and drive sustainable growth.
by Eric Koons
Eric is a passionate environmental advocate that believes renewable energy is a key piece in meeting the world’s growing energy demands. He received an environmental science degree from the University of California and has worked to promote environmentally and socially sustainable practices since. Eric’s expertise extends across the environmental field, yet he maintains a strong focus on renewable energy. His work has been featured by leading environmental organizations, such as World Resources Institute and Hitachi ABB Power Grids.
Read more