Japan’s Steel Industry: A Laggard For Decarbonisation
Source: SteelRadar
20 May 2024 – by Eric Koons
Today, Japan’s steel industry is the world’s third largest, producing over 85 tonnes annually. While most of the steel is used for domestic construction and automotive manufacturing, more than 25% is exported – making it one of the largest steel exporters in the world. This gives Japan’s steel industry significant influence in the global market.
The global steel industry has long been growing due to increasing market demand. As a result, greenhouse gas emissions associated with steel production have also been on the rise. The steel industry accounts for 9% of global carbon emissions. This directly results from the industry’s heavy reliance on fossil fuels during steel production.
Leading organisations, like the International Energy Association (IEA), highlight the industry as a critical sector to decarbonise to align with the Paris Agreement’s net-zero by 2050 goal. However, CO2 intensity related to steel production has only slightly decreased in recent years and is falling short of a net-zero pathway. A rapid shift away from coal blast furnaces in favour of low-carbon alternatives is critical to achieve carbon neutrality.
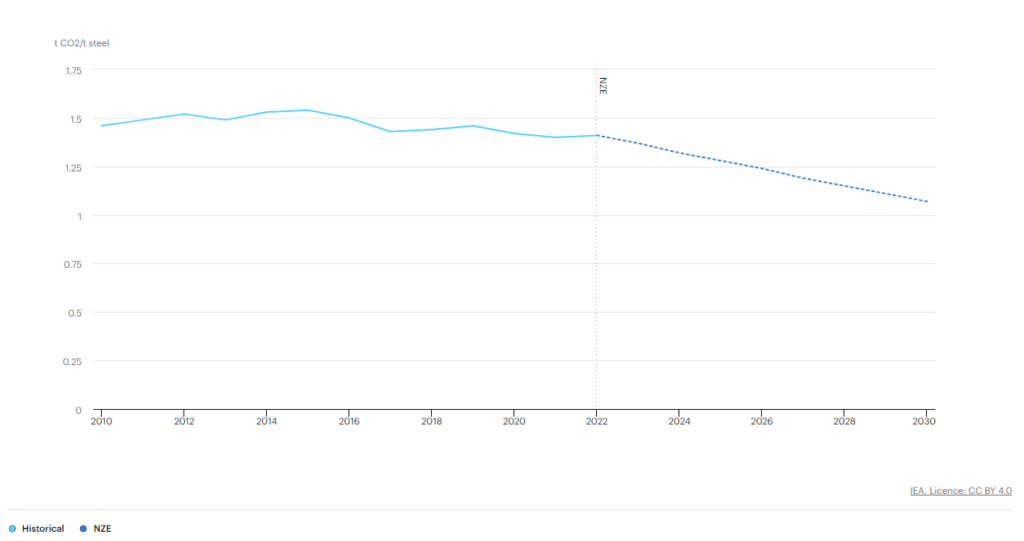
Emissions of Steel Industry in Japan
Japan’s steel industry emits approximately 114 million tonnes of carbon dioxide annually, contributing around 40% of the country’s industrial emissions and 14% of its total greenhouse gas emissions.
The reliance on coal-based blast furnaces for around three-quarters of Japanese steel production exacerbates the emissions intensity. This is worrying, as coal has the highest CO2 emissions co-efficient of common fossil fuels. Thermal coal accounts for 35% of the country’s total imports, with Japan being the world’s third-largest coal importer.
Japanese Steel Industry Versus National Decarbonisation
At present, Japanese steel industry is entirely reliant on coal for crude steel production. Acknowledging this, the industry has put forward its own decarbonisation goal of reducing emissions by 30% by 2030, compared to a 2013 baseline.
The Japanese steel industry already has the highest energy efficiency in the world, so emissions reductions will primarily rely on new production technologies. Integrating electric arc furnaces, which renewables can power, is one of the most viable pathways to reduce emissions. Other solutions, like green hydrogen-based blast furnaces, provide an alternative solution, but they are still in development and remain untested at scale.
The Japanese steel industry’s decarbonisation goal is a step in the right direction. However, it still does not align with the country’s decarbonisation goals of reducing emissions by 46% by 2030 and being net-zero by 2050. Furthermore, Japan’s decarbonisation goals are primarily seen as inadequate, highlighting how far behind the Japanese steel industry will be compared to other major producers. Japan remains the only G7 country not to implement a coal phaseout date and continues to hinder progress on a unilateral low-emissions steel transition.
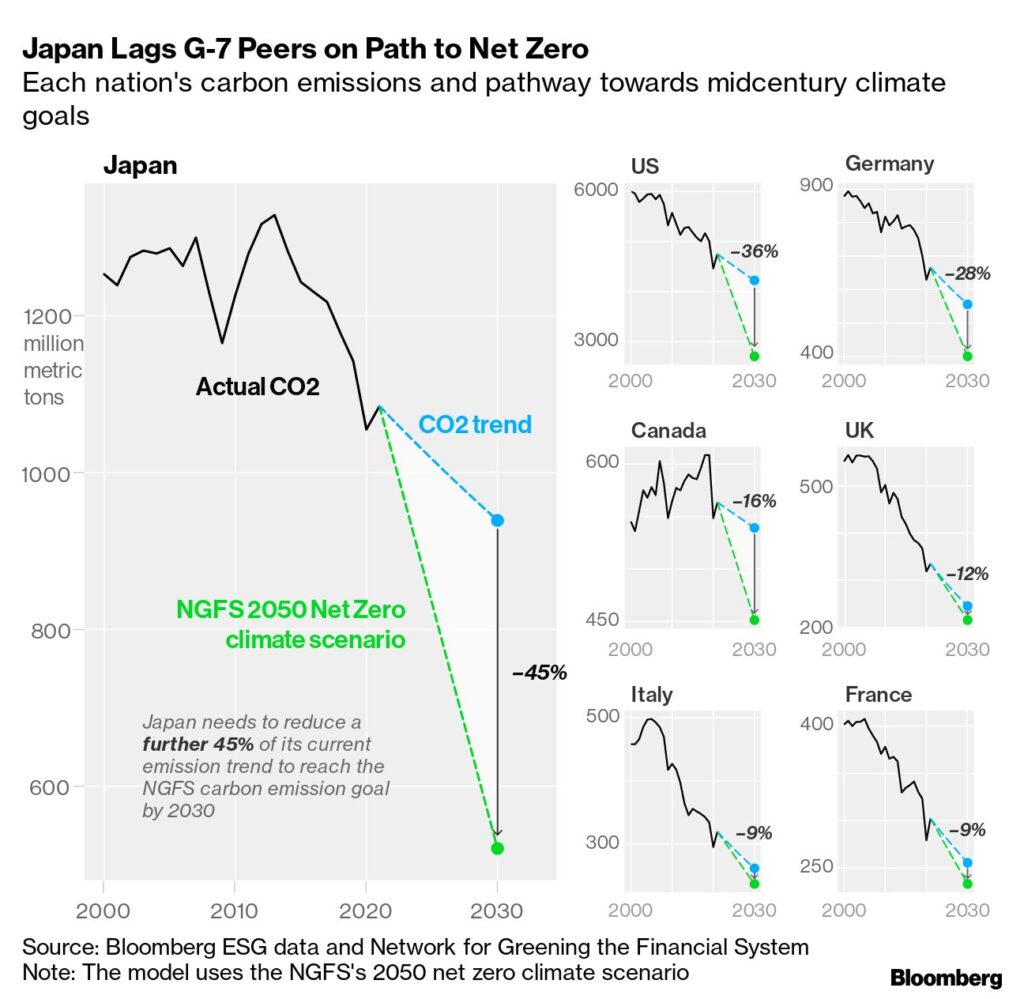
The Largest Steel Producer in Japan: Nippon Steel
Nippon Steel is at the core of Japan’s steel industry and its associated decarbonisation. Nippon is the Japan’s largest steel producer, producing 41.6 million tonnes in 2020. Nippon Steel operates 10 coal-blast furnaces in Japan, which results in a demand for over 23% of the country’s total coking coal import. As a result, the company produced over 75 million tonnes of CO2 in 2022.
As the largest steel producer in Japan and one of the largest in the world, Nippon Steel has significant sway in driving steel decarbonisation. The company influences local industry dynamics and has the capacity to finance innovation, which the industry needs to decarbonise.
Nippon Steel’s Decarbonisation Strategy
Nippon Steel aligns with the Japanese Steel industry’s goal of reducing emissions by 30% by 2030 and aims to be carbon neutral by 2050.
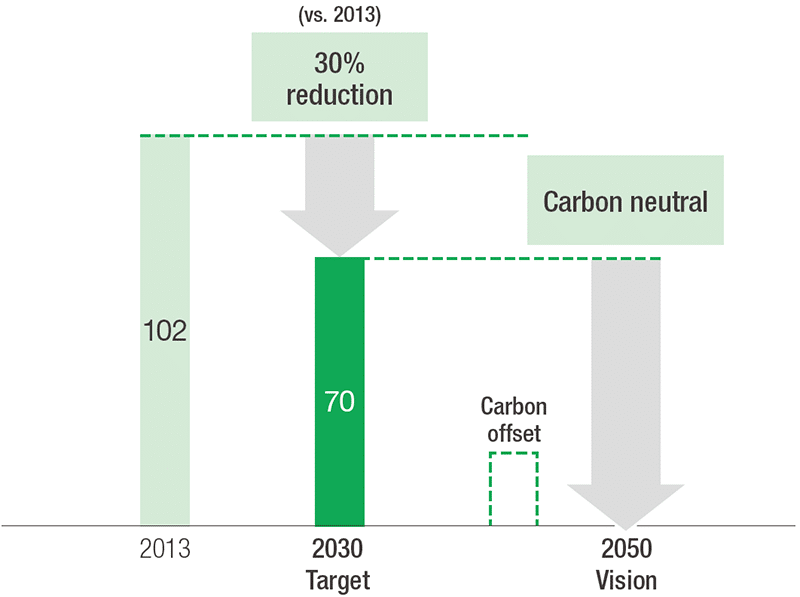
Its 2030 plan hinges on implementing hydrogen injection technology into existing blast furnaces, reducing emissions in existing processes and improving production efficiency. Hydrogen injection into coal-based blast furnaces will account for a 10% reduction in direct emissions and another 20% reduction from carbon capture and storage.
This reliance on hydrogen injection is concerning because it is still in the initial testing phase and is not implemented in large-scale facilities. Furthermore, it is inadequate compared to electric arc furnace technology, which is already mature and used widely around the world.
Its 2050 plan relies on implementing electric arc furnaces, 100% hydrogen blast furnaces and a combination of carbon capture and offsets. This approach seems more reasonable, yet it also has its concerns.
Typically, redeveloping blast furnaces happens at the end of their lifetime (15-20 years). Over half of the country’s blast furnaces require reinvestment by 2030, but Nippon Steel’s current 2030 plan does not intend to redevelop these facilities with electric arc technology. If this opportunity is missed, large-scale electric arc furnace redevelopment will likely not occur until between 2035 and 2040, dangerously close to the 2050 target.
Furthermore, the company has been investing in more international coal mines and is considering significant investments in Australia’s coal industry. This signals an unwillingness to shift away from coal and highlights major concerns about the pursuit of their stated decarbonisation goals.
Nippon Steel is being labelled as a climate laggard in the Asia region. Its current decarbonisation strategy does not align with the IPCC’s 1.5°C warming pathway or the IEA’s net-zero pathways.
Implications of Nippon Steel’s Poor Decarbonisation
Nippon Steel’s poor decarbonisation strategy poses significant challenges to Japan’s and the global steel industry’s efforts to mitigate climate change. With the industry facing increasing pressure to transition to low-carbon alternatives, Nippon Steel must lead by example and invest in proven technologies like electric arc furnaces. The company’s current trajectory, including investments in international coal mines, undermines its stated decarbonisation goals and risks exacerbating climate change.
This threatens national and global decarbonisation goals and puts Japan’s steel industry at risk. The demand for low-carbon steel is rising rapidly as industries and governments worldwide commit to reducing carbon emissions.
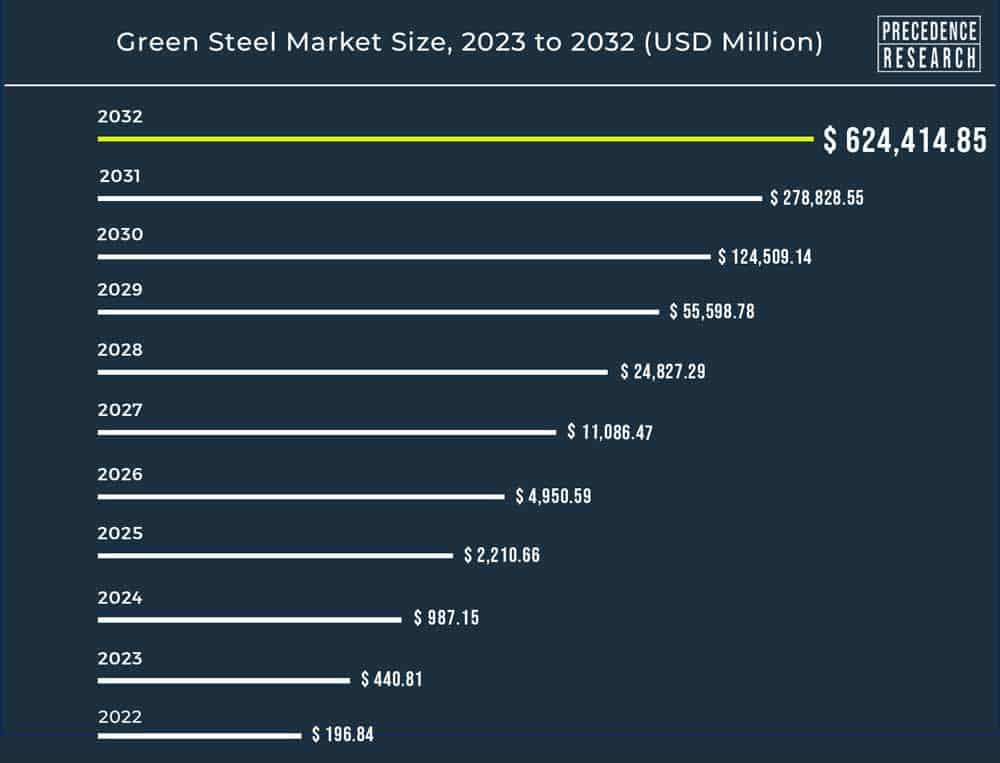
Countries are implementing carbon import tariffs, companies are committing to carbon-neutral value chains, and consumers are purchasing low-carbon products. Japanese steelmakers need to decarbonise to stay competitive in the global market. Embracing decarbonisation and investing in low-carbon steel production mitigates these risks and positions Japanese steelmakers as leaders in the global steel industry’s green transition.
by Eric Koons
Eric is a passionate environmental advocate that believes renewable energy is a key piece in meeting the world’s growing energy demands. He received an environmental science degree from the University of California and has worked to promote environmentally and socially sustainable practices since. Eric’s expertise extends across the environmental field, yet he maintains a strong focus on renewable energy. His work has been featured by leading environmental organizations, such as World Resources Institute and Hitachi ABB Power Grids.
Read more