Zero-carbon Cement: Is It Possible To Go Fossil-Fuel-Free?
26 July 2022 – by Dhra Dhirakaosal Naglis
Green solutions like electric vehicles and renewable energy are important in our fight against carbon emissions. While it is a much lesser-known innovation, zero-carbon cement has yet to become a household name despite its vast potential to reduce our carbon footprint.
This is because images of thick plumes of white smoke billowing from factories and car exhaust pipes often come to mind when we think about carbon emissions. Yet, cement, which is heavily relied upon in the construction of houses, buildings, roads, dams and underground infrastructure, is a top source of carbon emissions. Carbon free cement is the need of the hour to achieve net zero emissions.
The Cement Industry’s Gigantic Carbon Dioxide Footprint
The global cement industry accounts for about 7% to 8% of global carbon emissions – more than double that of the aviation industry’s global emissions. In 2021, the global cement production was 4.4 billion tonnes. If the industry were a country, it would rank as the third-largest carbon emitter after China and the US.
With rapid urbanisation and economic development in various parts of the world on the rise, the demand for cement has also risen. The industry expansion comes at a time when efforts are increasing globally to keep the temperature rise at 1.5°C and to achieve net-zero emissions by 2050.
Low-carbon Cement Technology – A Ray of Hope
Efforts have long been underway in the cement industry to reduce carbon emissions. But, the entry of tech companies and startups has helped expand the range of innovative solutions. This includes the use of green low-carbon cement technology, allowing companies to produce cement with lower carbon impacts. Their ultimate goal is the creation of fossil fuel free cement.
Solidia Technologies, a technology provider to to concrete and cement sector, is among these companies. It focuses on delivering sustainable technology for cement manufacturing and concrete curing.
Traditional Cement Production from Fossil Fuels and Its Heavy Carbon Footprint
To clarify, the traditional cement production process is the most carbon-intensive part. Fossil fuels enter a kiln that is over 1,400 °C to heat a mixture of clay and limestone. The unavoidable chemical reaction required to break down the limestone contributes to most of the carbon emissions.
How Concrete is Made?
The cement mixes with gravel, sand and water to make concrete – the planet’s most-used man-made resource. Cement acts as the glue that holds the concrete together, making it an essential component. Making one tonne of concrete emits about one tonne of carbon.
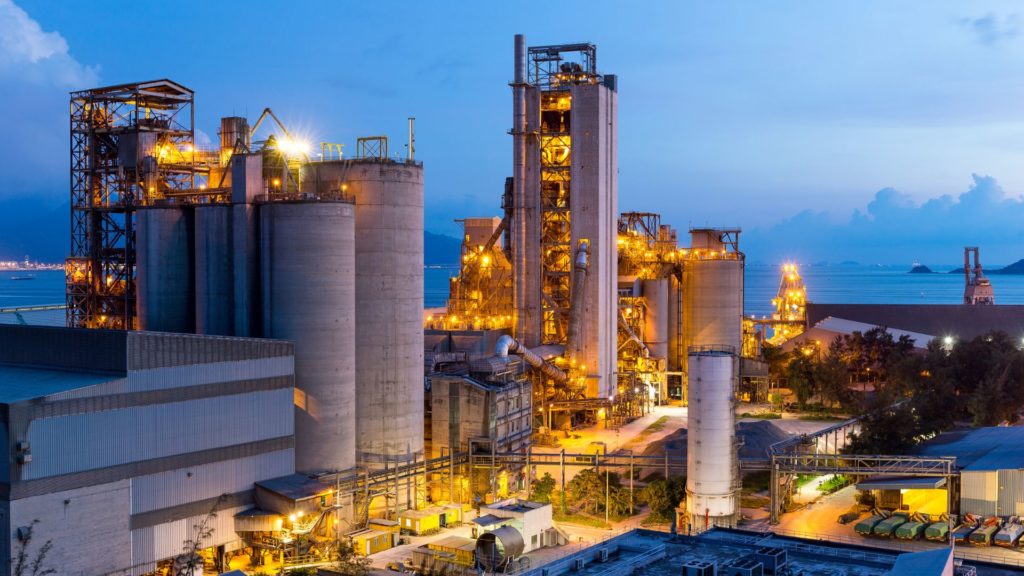
A New Cement Production Method – Lowering the Toll on the Environment
Solidia has created a type of cement that can be produced at lower temperatures. It claims to lower cement carbon emissions by up to 70%. The company came up with a production method that tweaks the cement-making recipe. However, all the raw materials are the same. The process uses less limestone, allowing the reaction to occur at a lower temperature of 1,200°C. This slashes carbon emissions and reduces the amount of energy needed by the kiln. It also created a different way to cure or harden cement by injecting carbon into its material structure instead of water. The process traps carbon in the final concrete product as the cement hardens.
Solidia’s low-carbon cement technology has garnered attention from key players in the industry, such as LafargeHolcim (now Holcim Group). It has resulted in a partnership between the two companies to reduce carbon emissions in building materials. Additionally, the US Department of Energy has provided a USD 2.1 million grant to Solidia to broaden its zero-carbon cement technology.
Progress Made But Laced with Questions
Still, it’s not easy for the cement industry, one of the world’s oldest industries, to go green. Cement and concrete have been a staple in construction for centuries – tried and tested for their durable qualities. Questions have arisen about whether the new technologies, such as carbon capture technology, are efficient enough to be used on a large scale. Such questions surround the conversion costs, regulatory tests and approvals and the limited number of production facilities. These issues raise doubts regarding this emerging zero-carbon concrete technology.
The Zero Carbon Concrete Market – Expansions on the Horizon
Yet, the green cement market is expected to grow even further. Big and small companies are moving forward with carbon-neutral cement initiatives, which include efforts by the world’s fourth largest cement producer – HeidelbergCement – to construct the planet’s first carbon-neutral cement plant by 2030. While Bill Gates’ climate finance firm recently led a USD 55 million round of funding for startup Brimstone, which aimed at commercialising the company’s carbon-negative cement business. Brimstone intends to do away with limestone, a major cause of carbon emissions.
While decarbonising the cement industry has many routes, whether through the use of green hydrogen as a substitute renewable-energy fuel, zero-carbon cement technology or alternative fuels, the transition needs to continue to move forward as net-zero emissions goals gain traction worldwide.