Green Steel: Powering The Low-carbon Economy
Source: MIT News
25 September 2024 – by Eric Koons
Green steel is a core component of decarbonising many industries that rely on steel as a core part of their supply chain. This includes industries such as automotive, construction and manufacturing, which have a growing number of net-zero emissions goals. These goals can’t be achieved without green steel.
Luckily, advancements like electric arc furnaces and hydrogen-based production methods are making green steel a viable alternative to traditional methods. As a result, companies like Volvo, Mercedes-Benz, BMW and Ford are integrating green steel into their businesses, setting the stage for competitors like Hyundai Motor Group to follow.
What Is Green Steel?
Green steel is steel that is produced without using fossil fuels during production. This results in significantly lower emissions associated with each kilogram of steel produced. While there is no threshold for how much greenhouse gas emissions reduction is required to qualify as green steel, companies have shown it is feasible to reduce emissions by over 95%.
Low-emissions steel should account for 95% of global steel production by 2050 to align with the International Energy Agency’s (IEA) net-zero roadmap and it is key to tackling climate change.
How Is Green Steel Made?
Green steel is primarily produced using renewable energy-powered electric arc furnaces (EAFs) and hydrogen-based production.
EAFs melt scrap steel using renewable electricity from sources like wind or solar. This process avoids the need for raw iron ore and coal, significantly reducing carbon emissions. EAFs also allow for flexibility in using recycled materials, cutting down energy consumption and waste.
Alternatively, hydrogen-based steelmaking replaces the carbon-intensive blast furnace process with green hydrogen. The purpose is to replace fossil fuels, reduce energy consumption and decarbonise steel making. Hydrogen acts as a reducing agent to separate pure iron from ore, producing water vapour instead of CO2. When powered by renewable energy, this method is nearly emission-free.
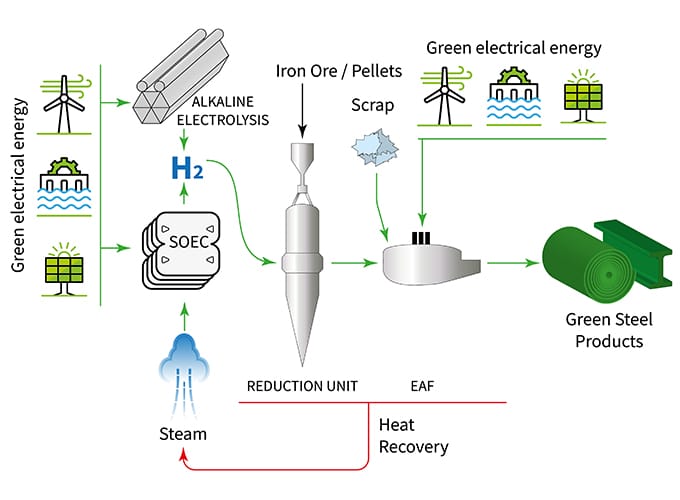
Both methods offer a path towards decarbonising steel production by reducing the production processes’ reliance on fossil fuels and coal. However, they have different applications. EAFs focus on recycling existing steel, while hydrogen steelmaking creates new steel with fewer emissions. Successful application of both processes is necessary for the industry’s decarbonisation.
The Cost of Green Steel
One of the main challenges for green steel is its cost. Currently, green steel is around 40% more expensive than traditional steel. This higher cost is primarily due to the need to scale up low-emissions steel technologies, production facilities and supply chains. This drives up both capital and operational expenses, which are passed on to the consumer.
However, as demand for low-emissions steel grows and economies of scale begin to take hold, experts predict that the price gap will narrow. Some projections show that low-emissions steel will be cost-competitive with traditional steel by 2035.
Why Can’t All Steel Be Green?
The entire steel industry will need to transition to low-emissions steel in the long term. However, this presents several challenges in the near-term.
Investment and Infrastructure Challenges
The steel industry is deeply entrenched in its current infrastructure, which relies heavily on coal-powered blast furnaces. EAFs only account for around 30% of global steel production, but expanding their use is critical to scaling green steel. However, building and retrofitting more EAFs requires significant capital investment.
Green Hydrogen Cost and Accessibility
One major hurdle in scaling green steel production is the limited availability and high cost of green hydrogen, which is crucial for hydrogen-based steelmaking. Currently, renewable hydrogen production is expensive, costing around USD 3-8 per kilogram, compared to USD 0.5-1.7 for conventional hydrogen.
Additionally, large-scale infrastructure for producing and distributing green hydrogen is still in development, and less than 1% of hydrogen produced today is green. Expanding green hydrogen capacity and lowering costs is essential. However, it requires an investment of USD 15 trillion by 2050 to scale up production to meet future demand for decarbonisation.
The Role of Green Steel and the Steel Sector
Green steel is essential in reaching global and sector-level net-zero goals – especially in carbon-intensive industries like automotive and construction. The IEA reports that the iron and steel sector must cut emissions by over 90% by 2050 to align with global climate targets.
These reductions will primarily come from renewable energy electrification and green hydrogen. However, the IEA notes that improvements in energy efficiency, reducing demand, shifts in production processes and carbon capture utilisation and storage (CCUS) are also critical steps.
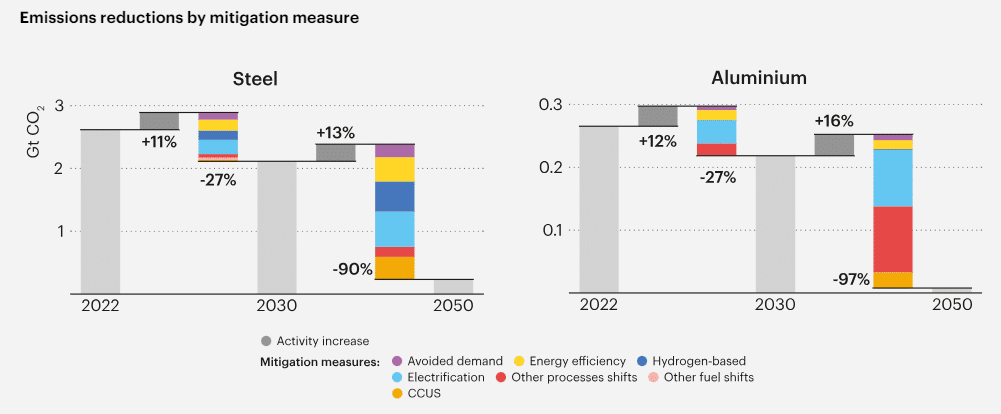
The Role of Steel Industry Leaders in Driving Low Carbon Emissions Steel Development
While challenges remain in scaling up production and managing costs, the long-term benefits of green steel are clear. Companies that commit to green steel are setting the standard for sustainability in their industries.
For example, Volvo has partnered with SSAB to bring green hydrogen-based steel to its production lines by 2026, with a goal of reducing overall emissions per car by 75% by 2030. This trend drives the demand for green steel, pushing steelmakers to innovate and reduce their carbon footprints.
Volvo’s stance is an example for other automotive companies. For these companies to meet their own net-zero goals, they must make similar commitments to green steel.
by Eric Koons
Eric is a passionate environmental advocate that believes renewable energy is a key piece in meeting the world’s growing energy demands. He received an environmental science degree from the University of California and has worked to promote environmentally and socially sustainable practices since. Eric’s expertise extends across the environmental field, yet he maintains a strong focus on renewable energy. His work has been featured by leading environmental organizations, such as World Resources Institute and Hitachi ABB Power Grids.
Read more